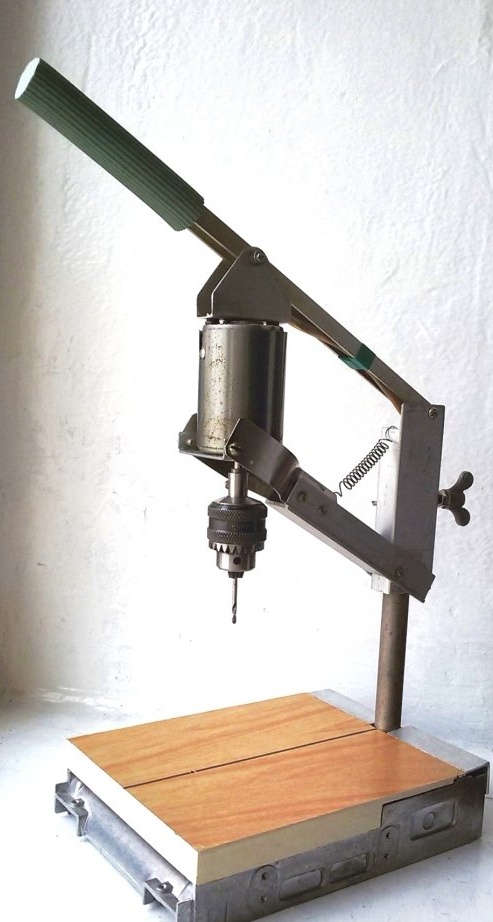
Si propone di realizzare una piccola perforatrice dal design molto semplice. Per la sua fabbricazione, le parti del modello non saranno necessarie: guide precise, cuscinetti volventi, meccanismi di movimento. Se nella tua casa c'è un piccolo motore per strumenti con un mandrino autoserrante sull'albero, puoi iniziare a lavorare. Realizziamo la macchina con materiali improvvisati. Le billette per i componenti non saranno difficili da trovare.
Caratteristiche del design.
Questa macchina è facile da fabbricare, ma presenta alcune limitazioni. Il suo design è progettato per praticare fori fino a 10 mm di profondità. Le capacità della macchina nel diametro di foratura e del materiale in lavorazione dipendono dalle caratteristiche (potenza, velocità di rotazione dell'albero) del motore elettrico utilizzato.
Una limitazione della profondità di perforazione è associata al design della sospensione della trasmissione. Il dispositivo si basa su un parallelogramma incernierato. Due parallelogrammi verticali di lunghezza uguale e collegamenti opposti, questo è il motore elettrico e la base della sospensione. I restanti due collegamenti uguali e opposti sono gli elementi di collegamento. Come sapete, in questo progetto, i collegamenti opposti saranno paralleli a qualsiasi rotazione dei collegamenti parallelogramma. Pertanto, l'asse comune del motore elettrico e della punta (nell'esatta fabbricazione di elementi a parallelogramma) sarà sempre parallelo all'asse del supporto fisso e perpendicolare alla tavola della macchina.
Per riferimento, un romboide è un parallelogramma in cui i lati adiacenti hanno lunghezze diverse e gli angoli non sono diritti.
Installazione e funzionamento della macchina.
La posizione dei collegamenti paralleli alla tabella verrà presa come posizione zero. Quando si lavora un pezzo su una macchina, per aumentare la precisione, la posizione di questi collegamenti dovrebbe avvicinarsi a una posizione orizzontale.
In questo caso, con il movimento assiale del trapano da +5 mm a -5 mm (corsa di 10 mm) dalla posizione zero delle maglie, l'offset radiale del trapano (nel piano romboidale) sarà di 0,08 mm. Questa quantità di spostamento avrà una lunghezza del collegamento di 150 mm. In pratica, questo spostamento è impercettibile e non sarà fondamentale per l'utensile e il foro da lavorare.
Quando si forano i circuiti stampati, anche con uno strumento in metallo duro fragile con un diametro di 0,8 mm, l'offset del trapano sulla scheda con uno spessore di 2 mm sarà di 0,003 mm (3 micron). Confronta il valore dato con l'offset e la posizione di questo trapano durante l'elaborazione manuale delle schede.
L'impostazione della macchina sulla dimensione del pezzo, in altezza, viene eseguita spostando rapidamente lungo il telaio della macchina manualmente, la base di sospensione e fissandola con una vite a testa zigrinata. L'altezza di sollevamento e fissaggio della base della sospensione è visivamente determinata dal rischio della posizione zero (tracciata sulla base della sospensione - l'ultima foto) quando si tocca la parte con la punta del trapano. Quando si perforano varie schede con uno spessore di 1 ... 3 mm, non è necessario un riaggiustamento in altezza.
Ulteriori vantaggi di progettazione.
La possibilità di installare schede di grandi dimensioni (con un aumento della sporgenza della punta, aumenta la precisione della perforazione).
Rilasciando la maniglia, al termine della perforazione, il motore con un trapano sotto l'azione della molla sale rapidamente e torna indietro di una distanza considerevole, liberando la zona di lavorazione del pezzo.
Nella posizione più alta, è possibile cambiare il trapano comodamente e rapidamente.
Penso che le caratteristiche di cui sopra parlino a favore della fabbricazione della macchina proposta. Il tempo speso per la fabbricazione di questo design di macchina ripaga di buon umore dall'esclusione di guasti di trapani costosi e scarsi.
1. Materiali e dettagli applicabili.
Motore elettrico e mandrino meccanico o a pinza.
Pezzi di una lamiera con uno spessore di 1,5 ... 2,0 mm.
Noleggio profilo in alluminio, tubo.
2. Fare una tavola di una perforatrice.
Prima di tutto, devi decidere sul tavolo della perforatrice. Le sue dimensioni, rigidità e resistenza determineranno l'accuratezza e la facilità d'uso. Esistono molti design di tavoli diversi. Nella data versione della macchina, viene utilizzato il caso del lettore CD, in attesa del suo uso secondario. Cassa rettangolare con dimensioni di 145 x 200 mm, in lega di alluminio. Ha un peso ridotto, una struttura rigida e planarità lungo la periferia della parte inferiore della parte, che conferisce una buona stabilità al prodotto futuro. Inoltre, questa parte non richiede praticamente alcuna elaborazione aggiuntiva. Per questi motivi, l'involucro è stato preso come base del tavolo della macchina.
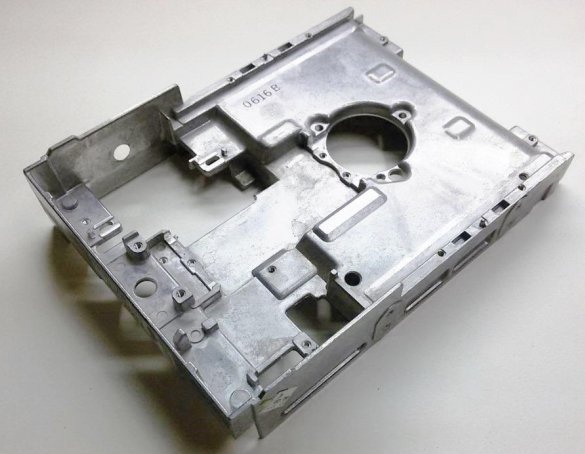
Una delle pareti corte (nella foto a sinistra), nel mezzo, ha un foro per il bullone M8, che determina automaticamente l'installazione del rack della macchina lì.
Come rack, puoi utilizzare laminati o tubi con un diametro di 18 ... 25 mm.
La struttura in esame utilizzava un tubo di acciaio a parete sottile con un diametro di 18 mm, che ha permesso di semplificare il metodo di fissaggio al tavolo.
Selezioniamo un bullone con una filettatura M8 e una testa, il cui diametro si adatta perfettamente al foro nel tubo (potrebbe richiedere un certo perfezionamento del diametro). Avvitare il dado sul bullone e premerli nel tubo. Lo stand è pronto. Resta da ripararlo sul tavolo con un secondo dado.
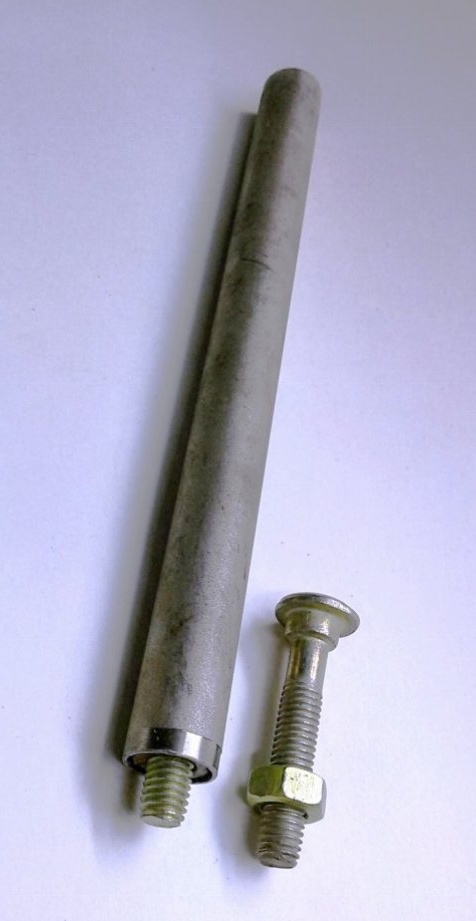
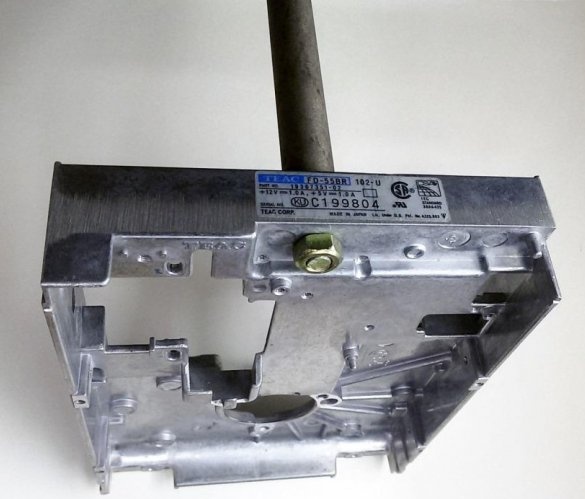
Sulla parte superiore del tavolo fissiamo il taglio del controsoffitto dal truciolato laminato lungo il contorno del corpo del pezzo. In questo caso, il supporto della macchina sarà inserito tra la parete dell'alloggiamento e il piano di lavoro. In futuro, sui lati liberi del rack fissiamo il rivestimento di un quadrato in alluminio. Tutto ciò fornirà ulteriore rigidità al rack installato.
Nel processo, controlliamo e, se necessario, adeguiamo la perpendicolarità del supporto della macchina al tavolo.
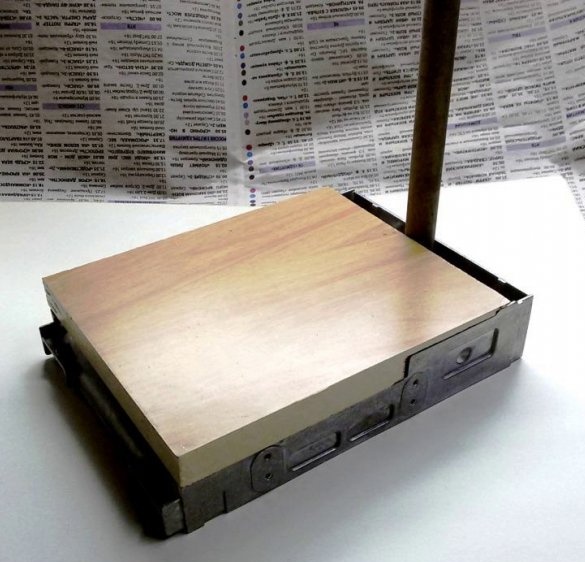
3. Rendere la base della sospensione.
La base di sospensione è necessaria per installare il meccanismo a parallelogramma articolato sul supporto della macchina. Serve come parte integrante del romboide, lo fissa sul rack, all'altezza desiderata e ad un angolo selezionato dal bordo del tavolo. Il profilo in alluminio sagomato (18 x 40 mm), che in precedenza fungeva da maniglia per porta del mobile, veniva utilizzato come base per la sospensione.
Nel mezzo di una sezione del profilo, circa due lunghezze del motore elettrico, facciamo un foro e tagliamo una filettatura M6 o M8 sotto la vite di fissaggio. Controlliamo l'affidabilità dell'installazione della base di sospensione sul rack della macchina.
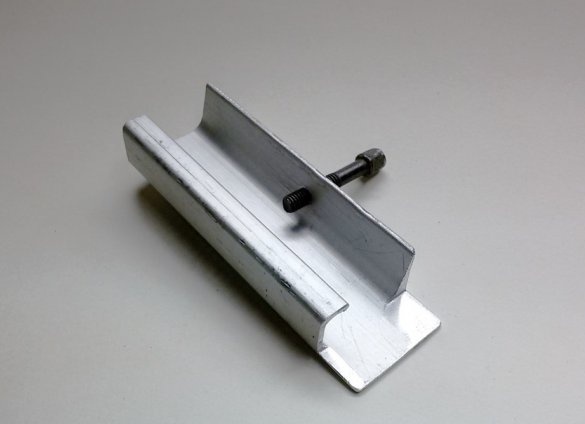
Fabbricazione di un meccanismo per il montaggio di un motore elettrico
4. Supporto motore inferiore.
Per la perforatrice proposta è stato utilizzato un motore DC con magneti permanenti DC 24V, 0,7A.
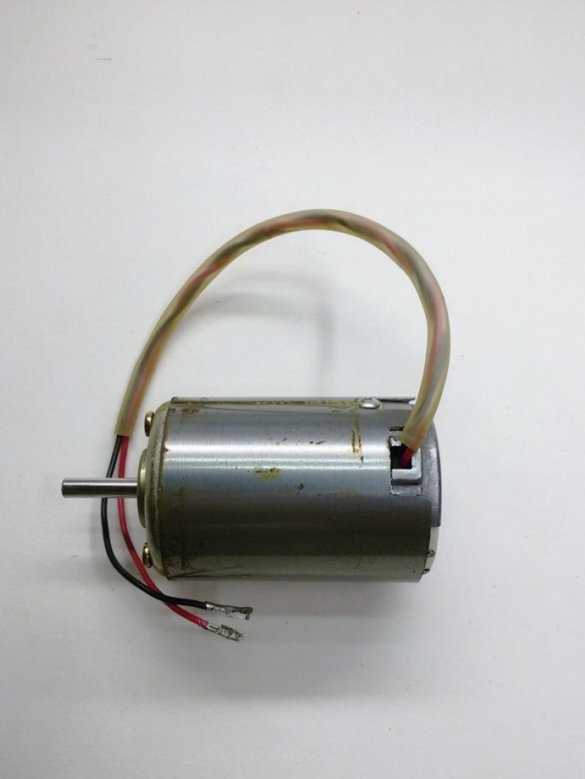
Iniziamo la produzione del parallelogramma articolato con il collegamento principale, costituito da un motore elettrico e dai suoi elementi di fissaggio. Le dimensioni del motore utilizzato possono essere diverse, così come la posizione dei fori di montaggio. Pertanto, le dimensioni dei dispositivi di fissaggio non sono indicate.
Da una lamiera di acciaio con uno spessore di 1,5 ... 2,0 mm, produciamo il supporto motore inferiore. Negli scaffali laterali del supporto, praticare fori coassiali e tagliare il filo M4 in essi. Installare il supporto motore con due viti standard.
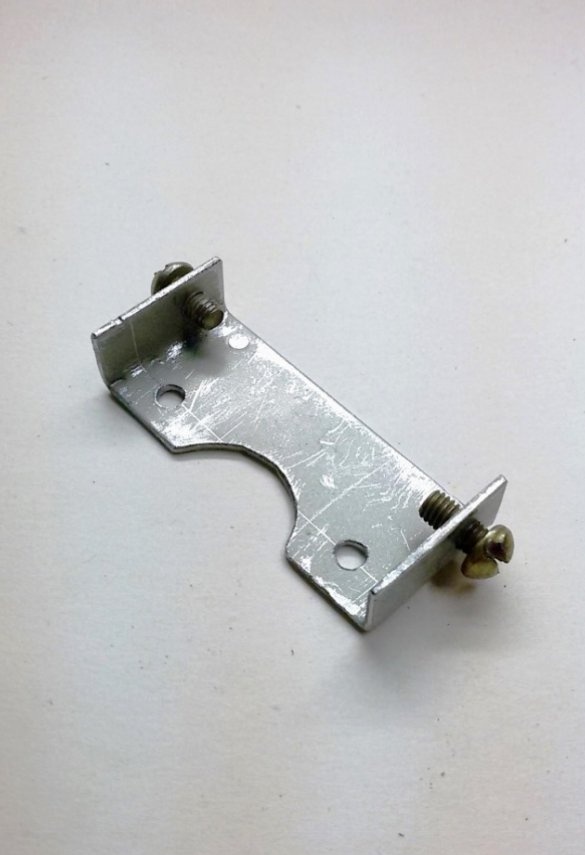
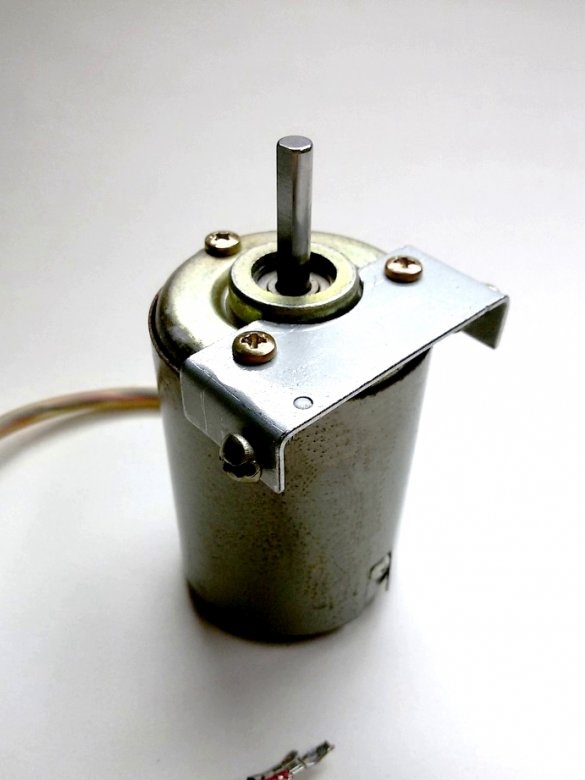
5. Il collegamento inferiore del parallelogramma.
Renderemo disponibile il collegamento inferiore del parallelogramma in alluminio laminato. Ad esempio, nella progettazione proposta, è stato utilizzato un profilo in alluminio a forma di U (20 x 20 mm), che era precedentemente utilizzato nella produzione di finestre.
Per collegare il braccio inferiore con il supporto del motore, da una lamiera di acciaio con uno spessore di 1,5 mm, produciamo due elementi di transizione realizzati a specchio. Sono rigidamente collegati al profilo del collegamento con due viti (rivetti).
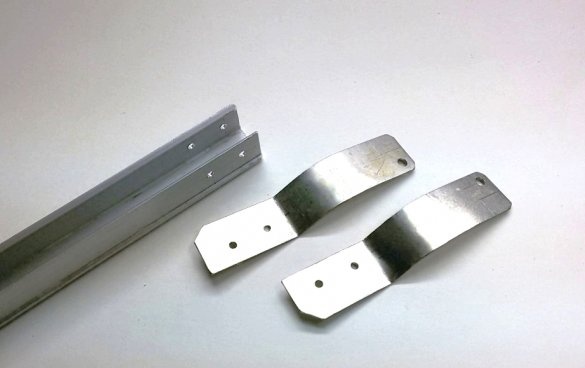
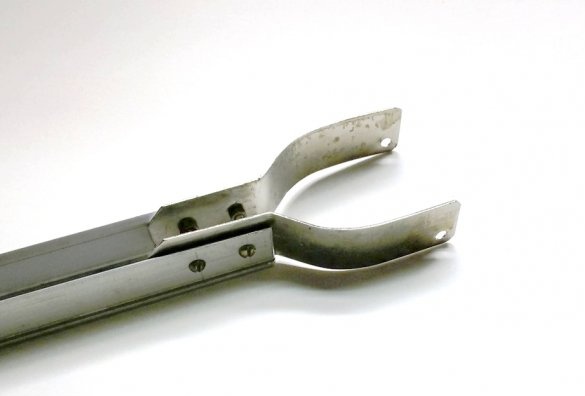
6. Braccio inferiore con supporto motore
La lunghezza del braccio inferiore è determinata dalla dimensione del tavolo fabbricato. In questo modello, questa lunghezza (la distanza tra gli assi dei fori di montaggio) è definita come 150 mm. Contrassegnare i fori per il collegamento alla base della sospensione e tagliare il profilo nella dimensione desiderata. Se necessario, sul lato tagliato del profilo, formiamo la larghezza della scanalatura per una connessione stretta in larghezza con la base di accoppiamento della sospensione. Eseguiamo i fori coassiali di marcatura.
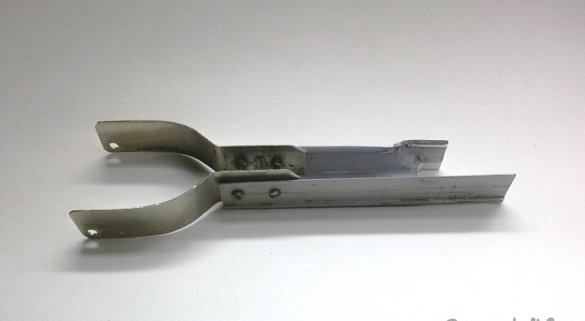
Montiamo il braccio inferiore con il supporto del motore elettrico. Usando le viti M4, fissiamo il braccio inferiore al supporto del motore, assicurando una rotazione libera nella connessione. La posizione del foro della cerniera nel braccio inferiore, dietro il motore, è dettata dal massimo aumento possibile della lunghezza del braccio, aumentando quindi la precisione dell'elaborazione.
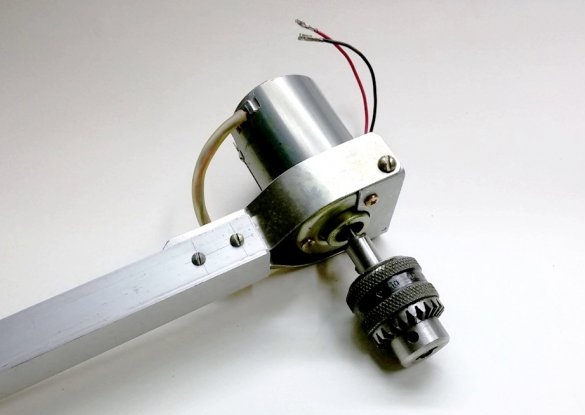
7. Supporto motore superiore.
Da una lamiera di acciaio o alluminio con uno spessore di 1,5 ... 2,0 mm, produciamo il supporto motore superiore. Il design della parte dipenderà dalla posizione dei punti di attacco sul motore esistente. Installare il supporto motore superiore.
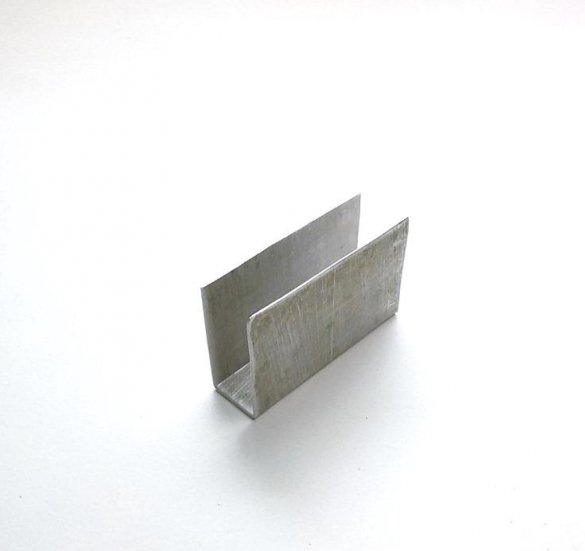
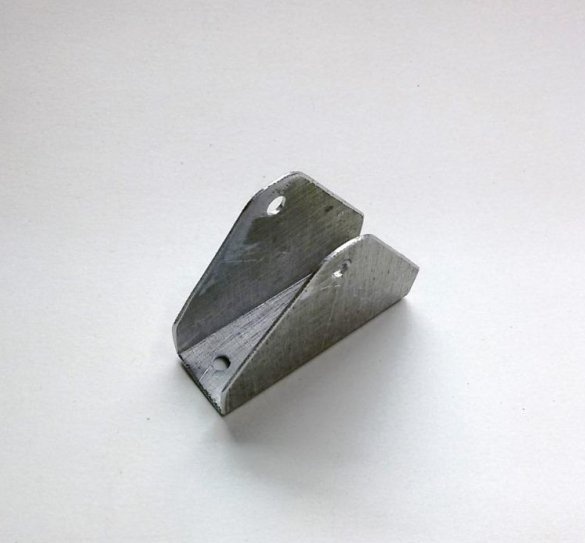
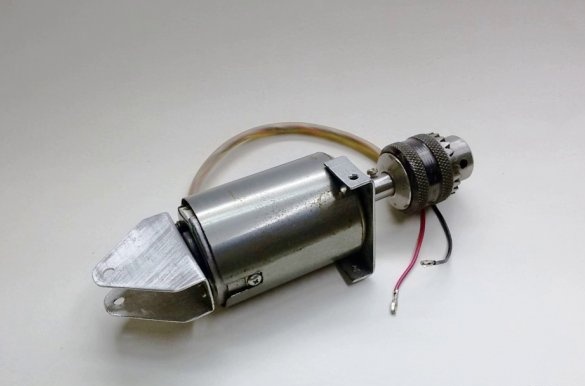
8. Il collegamento superiore del parallelogramma.
Anche il collegamento superiore del parallelogramma è realizzato in alluminio laminato. Ad esempio, il design proposto utilizzava un profilo in alluminio a forma di H (12 x 16 mm). Contrassegnare il pezzo del collegamento superiore. Trasferiamo la distanza tra gli assi dei fori di montaggio del braccio inferiore prodotto sul pezzo del braccio superiore. Praticare i fori per la marcatura. La lunghezza del pezzo del collegamento superiore, è desiderabile raddoppiare, rispetto alla dimensione di lavoro del collegamento. Useremo l'estremità libera del profilo come maniglia per alimentare il trapano, che ridurrà della metà la forza della mano. Un pezzo di tubo di plastica può essere posizionato su questa parte del pezzo.
La distanza tra gli assi dei fori di montaggio e la loro posizione sui supporti del motore, trasferiamo alla base della sospensione. In altre parole, nel parallelogramma prodotto, le linee che collegano gli assi dei fori di montaggio sui supporti del motore e la base delle sospensioni devono essere uguali e parallele.
Per soddisfare questa condizione, nella progettazione della macchina prodotta, parte del profilo viene ritagliata sulla base della sospensione (nella parte superiore).
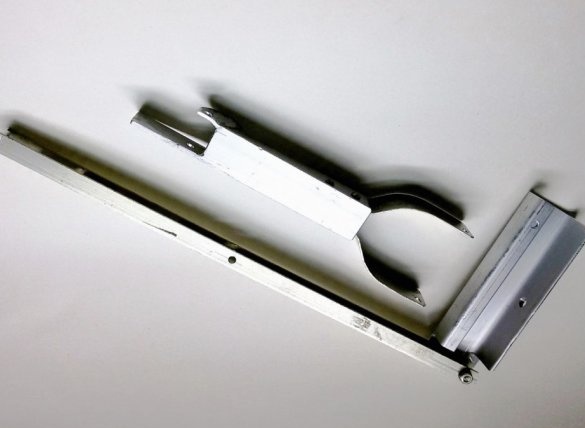
9. Assemblaggio del parallelogramma articolato - romboide.
Montiamo un romboide, lo installiamo su un rack e controlliamo il meccanismo in funzione.
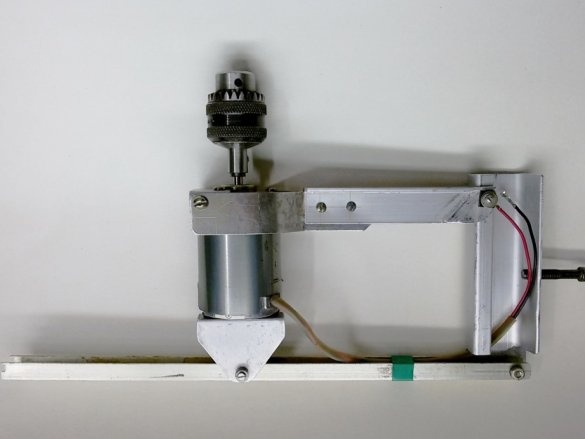
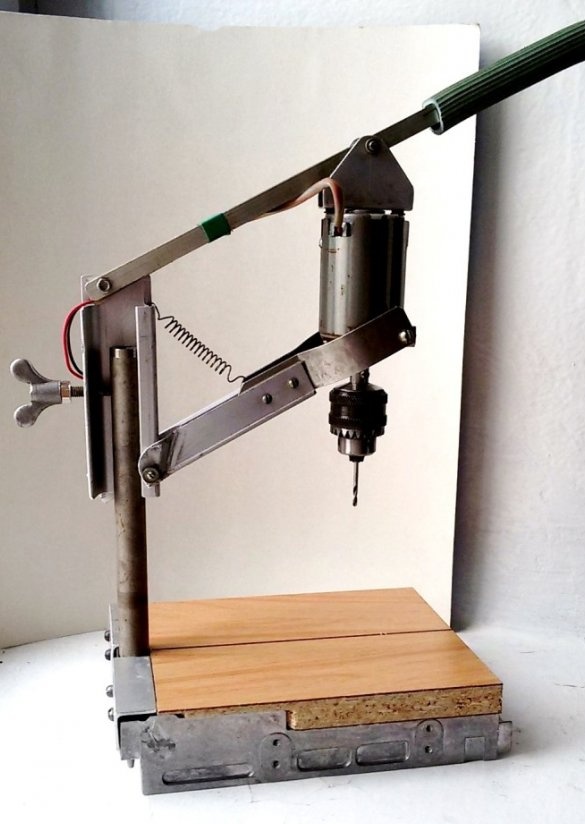
10. Controllo dell'accuratezza del meccanismo
di ortogonalità
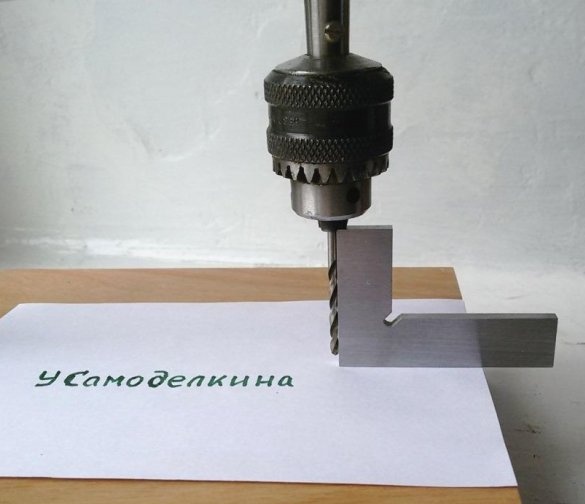
per trapani con una corsa di 10 mm
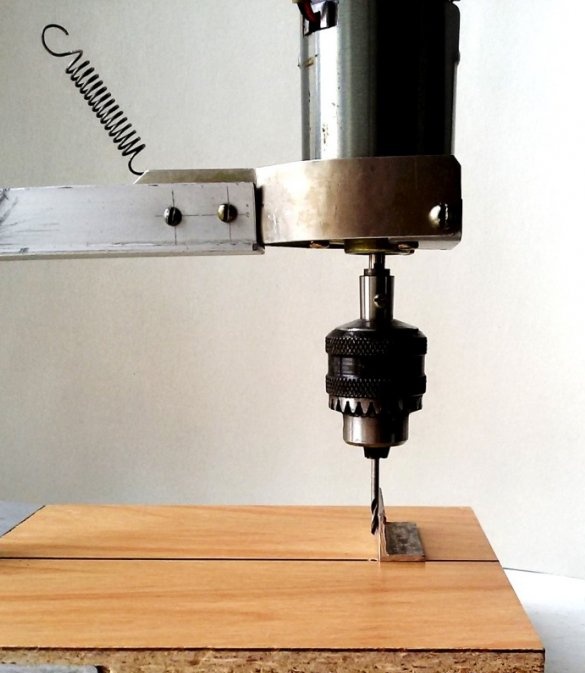
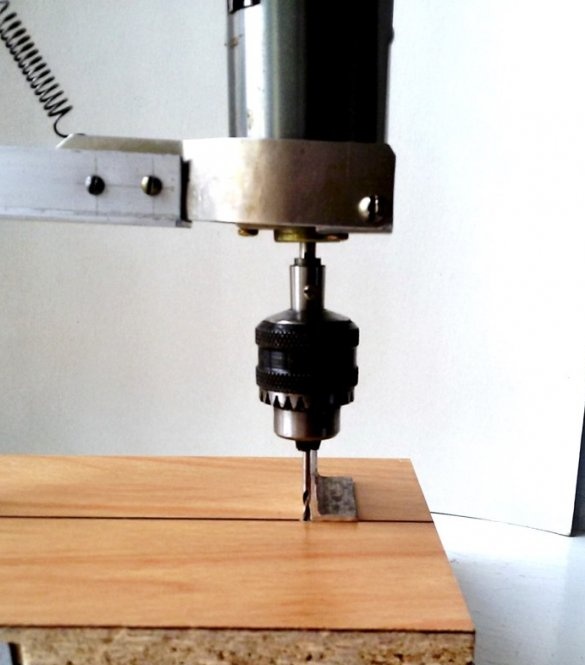
sotto carico.
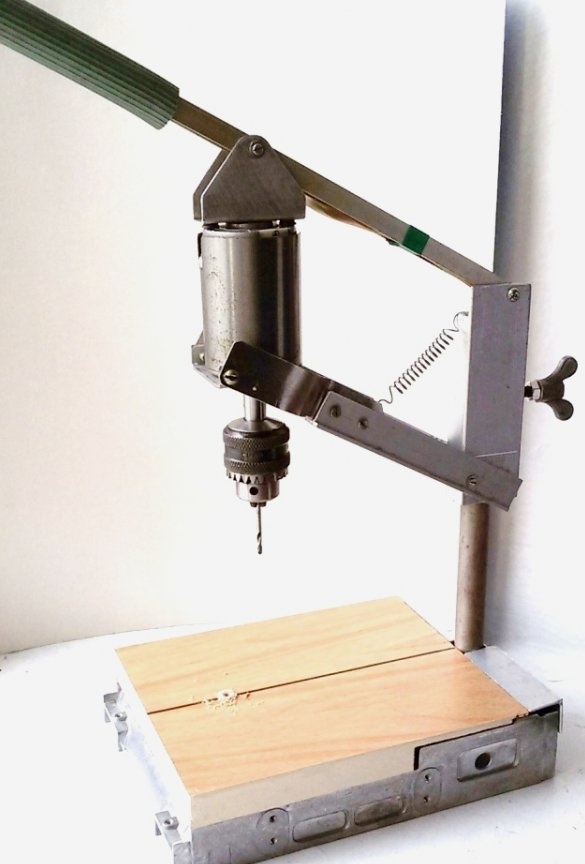